It is cheap, ecological and available, …
So why is straw used so little in building?
It grows in less than a year, stores CO₂ for decades and comes as a cheap by-product from agriculture. Just 60% or the straw that the Austrian farmers produce, would be enough to isolate the entire building production of that year. Still it remains a niche product, something of the past. Why is straw used so little? How can it be applied? What is possible inside the building regulations? We learned more in a public discussion evening that we organized about the matter. Spoiler alert: strong lobby of interest groups hinder a wider application of straw.
Theory, practice and an eager curiosity came together during the Echoraum on organic isolation materials. We ourselves as organizers and the numerous visitors took care of the curiosity, while an expert on straw isolation techniques brought in practice experience. Theoretical input from the highest level, came from the professor who leads the university course on sustainable construction in the Technical University of Vienna. She sketched the use and application of different organic materials in isolation. It was a rich learning experience that gives hope for the knowhow of future generations of architects.
Using old materials in new buildings
In many of the examples we heard of, straw is combined with mud plaster. In prefab elements the components for electricity and heating can be put in beforehand, to facilitate the work on site. Besides isolation material, straw can be used constructively as well, up to two stories. There are numerous examples of interesting projects built with straw bales: so much that in Austria they even have their own network. Unfortunately though the website of the ‘Austrian straw bale network’ is in German only, different from what the name would suggest.

Straw is mostly used pressed together in prefab elements, or it can be blown into the construction. In some specialised applications it is pressed together on the spot. Compacting is needed to increase fire safety. That obviously is a point that requires a careful design. In fact, the good environmental qualities of the material have been a bit in the shadow of this vulnerability to fire, as well as to humidity or pests, hence its reputation as a “complicated” material.
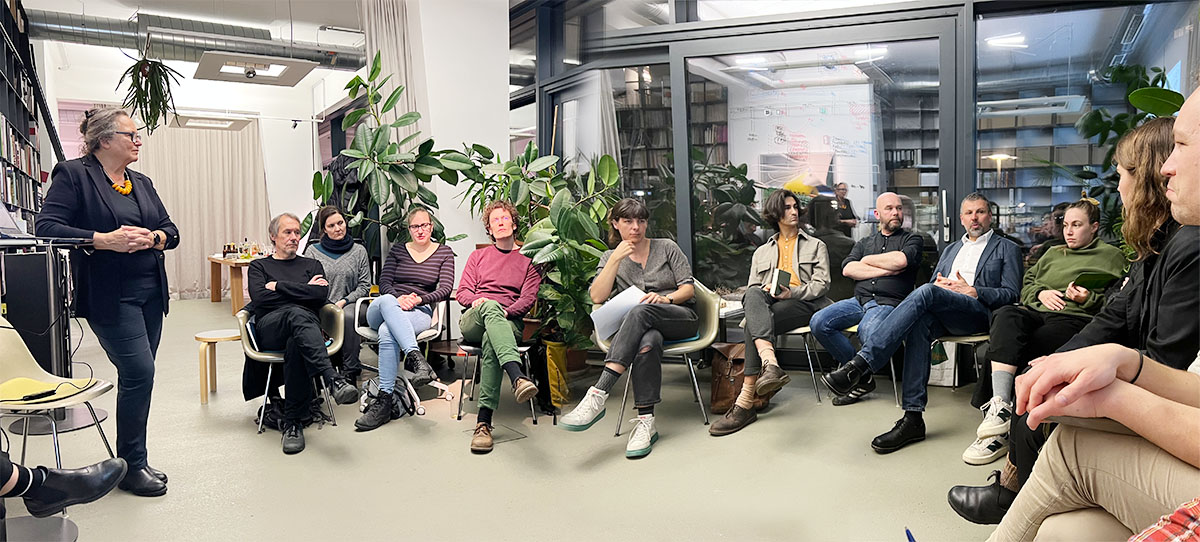
How lucky we were to get input into the discussion from the renowned TU Vienna Expert on sustainable building, Prof. Dr. Karin Stieldorf. Photo: Vis-à-Wien
Why does straw have such a bad press?
Most architects have not learned about applying organic isolation materials and product information is not so easy to obtain. Producers of sustainable isolation materials need time and money to obtain an eco-certificate. Paradoxically enough the large industries that produce synthetic isolation, often do have one, even if these products have a large CO₂ footprint. Most of all, straw does not have a good lobby, to make it land favourably in the handbooks that technicians use. The material is simply not in the awareness of those involved in building, be it architects, developers or authorities. This changes only slowly, though there are shimmers of hope.
For the time being, non-organic isolation materials like polystyrene, have a powerful lobby of producers, who use their influence to establish the norms used in construction. For instance, the method used to calculate the isolation value of straw, stipulates to count with relatively humid straw, that does not isolate as well as dry straw. The result is a rather thick wall and less net floor space, which gives less return on investment than a thinner wall isolated differently.

Practical perspectives were given by Reinhard Appeltauer from Sonnenklee, a business specialised in straw isolation: Photo: Vis-à-Wien
Interestingly enough, this is not so much the case in all of Austria. Vorarlberg has more of an ecological building culture. Developers there, are not as much focused on the returns per square metre usable surface. They count with the total surface, including the construction. Or there is another consciousness, that also puts value to aspects like the microclimate in the building, human health and sustainability. Hopefully this mindset spreads out over the rest of the country.